Маховик
* Проверьте состояние зубчатого венца и в случае повреждения его зубьев маховик замените. На поверхности маховика, прилегающей к фланцу коленчатого вала, и на поверхности под ведомый диск сцепления не допускаются царапины и задиры. Неплоскостность поверхности должна быть не более 0,06 мм.
* Царапины и задиры на поверхности удаляйте проточкой, снимая слой металла толщиной не более 1 мм. При проточке необходимо обеспечить параллельность поверхностей 2 и 3 относительно поверхности 1 (рис. 1). Допускаемая непараллельность — не более 0,1 мм. 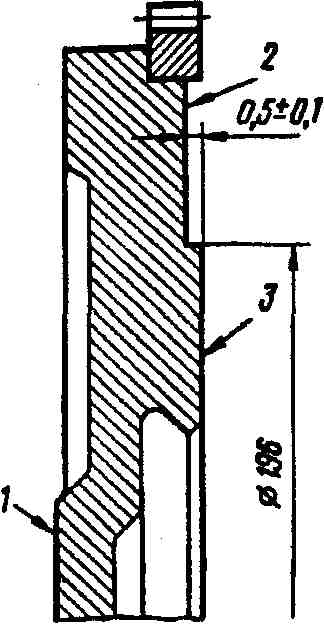
Рис. 1. Проверка маховика
* Устанавливайте маховик на оправку, центрируя его по посадочному отверстию и проверяйте биение плоскостей. При замене маховика балансировать его не требуется.
Головка блока цилиндров и ее детали Головка блока цилиндров
* Тщательно промойте головку блока цилиндров и очистите масляные каналы. Удалите нагар из камер сгорания и с поверхности выпускных каналов металлической щеткой.
* Осмотрите головку цилиндров. На постелях под шейки распределительного вала и в отверстиях под толкатели клапанов не должно быть задиров и повреждений.
* При подозрениях на попадание охлаждающей жидкости в масло проверьте герметичность головки блока цилиндров.
* Для проверки герметичности закройте отверстия охлаждающей рубашки заглушками и нагнетайте насосом воду под давлением 5 кгс/см2. В течение 2 мин не должно наблюдаться утечки воды из головки цилиндров.
* Можно проверить герметичность головки блока цилиндров сжатым воздухом, для чего заглушите отверстия охлаждающей рубашки заглушками приспособления для проверки головки цилиндров на герметичность, опустите головку цилиндров в ванну с водой, подогретой до 60—80°С, и дайте ей прогреться в течение 5 мин. Затем подайте внутрь головки сжатый воздух под давлением 1,5—2 кгс/см2. В течение 1 — 1,5 мин не должно наблюдаться травления воздуха из головки.
Седла клапанов
* На рабочих фасках седел в зоне контакта с клапанами не должно быть точечных раковин, следов коррозии и повреждений.
* Если имеются наплывы металла по внутреннему диаметру седла, в зоне рабочей кромки, то удалите их фрезами для обработки седел выпускных клапанов (для выпускного клапана) и обработки седел впускных клапанов (для впускного клапана), выдерживая размеры Ж 27,6 и Ж 31 мм. Фрезы надевайте на шпиндель фрез для обработки седел клапанов и центрируйте направляющими стержнями из комплекта направляющих стержней для обработки седел клапанов.
* Проверьте герметичность клапанов, для чего тщательно очистите седла и клапаны, установите в головку цилиндров клапаны с пружинами и залейте керосин во впускные и выпускные каналы головки цилиндров. При выдержке в течение 3 мин не должно наблюдаться течи керосина через клапаны.
* В случае негерметичности клапанов притрите их к седлам с помощью притирочной пасты и оправки с резиновой присоской или специальной дрели, поворачивая клапан попеременно в обе стороны относительно его положения в головке. Это положение следует пометить и сохранять при установке клапана.
* Во время притирки под клапан рекомендуется устанавливать отжимную пружину с малой упругостью.
* После притирки тщательно удалите с седел и клапанов следы притирочной пасты, промойте и продуйте их сжатым воздухом.
Клапаны
* Удалите нагар с клапанов. Проверьте, не деформирован ли стержень (непрямолинейность стержня не более 0,015 мм) и нет ли трещин на головке клапана.
* Поврежденный клапан замените.
* Проверьте состояние рабочей фаски клапана. При мелких повреждениях ее можно прошлифовать, выдерживая угол фаски 45°30'±5'.
Направляющие втулки клапанов
* Проверьте зазор между направляющими втулками и стержнями клапанов, измерив диаметр стержня клапана и отверстие направляющей втулки. Если зазор больше допустимого, замените клапан.
* Если чрезмерный зазор не устраняется только заменой клапана, замените и направляющую втулку. Для этой операции пользуются оправкой для выпрессовки и запрессовки направляющих втулок, запрессовывая втулки с надетым стопорным кольцом до упора его в тело головки цилиндров.
В запасные части направляющие втулки поставляются с увеличенный на 0,02 мм наружным диаметром и с припуском по внутреннему диаметру. Поэтому после запрессовки разверните отверстия в направляющих втулках развертками для направляющих втулок клапанов для втулок впускных клапанов и развертками для направляющих втулок клапанов для выпускных.
* Затем проверьте герметичность клапанов и при необходимости притрите клапаны к седлам.
Маслоотражательные колпачки направляющих втулок
* У маслоотражательных колпачков не допускаются отслоение резины от арматуры, трещины и чрезмерный износ рабочей кромки. При ремонте двигателя маслоот-ражательные колпачки рекомендуется всегда заменять новыми.
* Заменять поврежденные колпачки желательно на снятой головке цилиндров, чтобы не погнуть стержни клапанов. Для напрессовки колпачков пользуйтесь оправкой для установки маслоотражательных колпачков клапанов. Есть, впрочем, способы замены колпачков и без снятия головки, когда в свечное отверстие закачивается сжатый воздух, чтобы клапаны не провалились в цилиндр.
Пружины и толкатели
* Пружины контролируйте на упругость и наличие трещин. Упругость пружин клапанов проверяйте подлине пружины в свободном состоянии (44,7 мм наружная и 35,2 мм внутренняя) и под нагрузкой: 26 и 47,4 кгс для наружной (при этом длина должна быть соответственно 33,7 и 24,7 мм); 11 и 29 кгс для внутренней (при этом длина соответственно 29,7 и 20,7 мм).
* Проверяйте состояние рабочей поверхности толкателя. На ней не должно быть задиров и царапин. При повреждениях толкатель заменяйте.
Регулировочные шайбы, болты крепления головки цилиндров
* Рабочие поверхности шайб должны быть гладкими, без забоин, царапин и задиров. На них не должно быть ступенчатого или одностороннего износа, натира металла. Допускаются концентричные следы от приработки с кулачками распределительного вала.
* При многократном использовании болтов крепления головки цилиндров они вытягиваются. Поэтому проверяйте, не превышает ли длина болта 135,5 мм (без учета высоты головки болта), если она больше, то замените болт новым.
Распределительный вал и его привод Распределительный вал
* На опорных шейках распределительного вала не допускаются задиры, забоины, царапины и наволакива-ние алюминия от опор. На рабочих поверхностях кулачков и эксцентрика не допускаются любые повреждения и следы износа в виде огранки.
* Установите распределительный вал крайними шейками на две призмы, помещенные на проверочной плите, и замерьте головным индикатором малых перемещений радиальное биение остальных шеек, которое не должно превышать 0,02 мм.
Опоры распределительного вала
* У опор трещины в любых местах не допускаются. На опорных поверхностях под шейки распределительного вала не должно быть задиров и царапин.
* Проверьте зазор между шейками распределительного вала и отверстиями опор. Зазор определяется расчетом после промера шеек и отверстий в опорах на головке блока цилиндров с установленными крышками опор. Если зазор больше 0,2 мм, то головку цилиндров с опорами следует заменить.
Зубчатый ремень
* Поверхность зубчатой части должна быть с четким профилем зубьев, без складок, трещин, подрезов и отслоений ткани от резины. На любой поверхности ремня не допускаются следы попадания масла. На торцовых поверхностях не должно наблюдаться расслоения и разлохмачивания, но незначительное выступание бахромы ткани допускается. Поверхность наружной плоской части должна быть ровной, без складок, трещин, углублений и выпуклостей.
Система охлаждения Водяной насос
* Удалите отложения с крыльчатки, корпуса и промойте детали. Проверьте осевой люфт подшипника с валом, который не должен превышать 0,13 мм при нагрузке 5 кгс. При большем люфте подшипник с валом замените новыми. Деформации и трещины на корпусе не допускаются.
* Сальник насоса и прокладку между насосом и блоком цилиндров рекомендуется заменять после снятия и разборки насоса новыми.
Электровентилятор радиатора
* Вентилятор должен включаться при работающем двигателе после перехода стрелки указателя температуры охлаждающей жидкости в красную зону шкалы. Если вентилятор не включается, это указывает на неисправности датчика включения электровентилятора, реле включения или самого электродвигателя.
Радиатор
* После снятия радиатора проверьте его герметичность в ванной с водой. Для этого закройте патрубки радиатора и подведите в него сжатый воздух поддавлени-ем 1 кгс/см2. Опустите радиатор в воду не менее чем на 30 с. При этом не должно быть травления воздуха.
* Герметичность можно проверять и без снятия радиатора с автомобиля. Для этого при заглушенных патрубках радиатор заполните водой под давлением 1 кгс/см2. Течи не должно быть. Чтобы создать это повышенное давление, иногда в радиатор закачивают воздух.
* При повреждениях или негерметичности замените радиатор или отремонтируйте. При повреждении алюминиевой трубки разберите радиатор и на стенде рассверлите дефектную трубку с двух сторон сверлом 8,5 мм на глубину 25—30 мм. В дефектную трубку вставьте развальцованную с одного конца ремонтную трубку диаметром 7,3 х 0,5 мм и на специальном стенде произведите дорнование (продавливание) трубки стальным дорном 7,5 мм по всей длине трубки. Затем на стенде для расширения трубок произведите расширение ремонтной трубки одновременно с двух концов. Соберите радиатор и проверьте его герметичность.
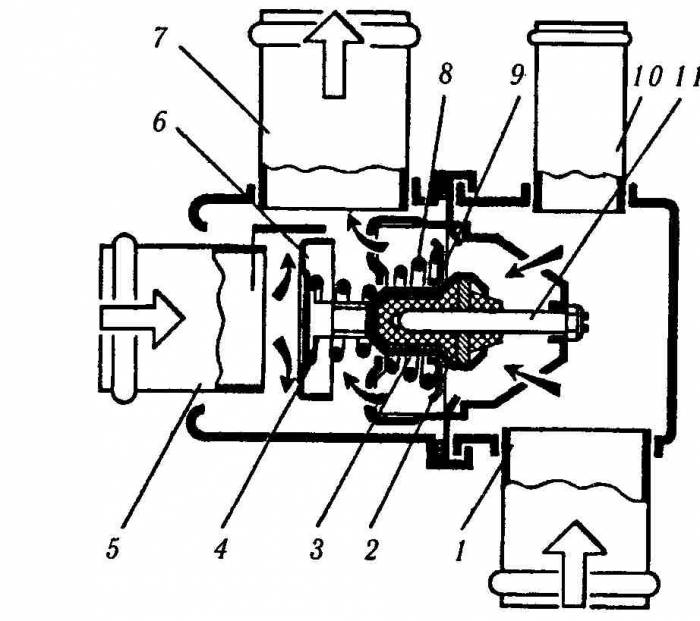
Рис. 2. Термостат:
1 — входной патрубок (от радиатора); 2 — резиновая вставка; 3 — твердый термочувствительный наполнитель; 4 — пружина дополнительного клапана; 5 — входной патрубок; 6 — перепускной клапан; 7 — выходной патрубок (к насосу); 8 — пружина основного клапана; 9 — основной клапан; 10 — патрубок (от расширительного бачка); 11 — поршень.
* Допускается глушение не более 1,5% охлаждающих трубок (обязательно с обоих концов).
Термостат
Устройство термостата показано на рис. 2.
* У термостата проверьте температуру начала открытия основного клапана и ход основного клапана. Термостат установите на стенде и опустите в бак с техническим глицерином. Снизу в основной клапан уприте кронштейн ножки индикатора. Начальная температура глицерина в баке должна быть 78—80 °С. Температуру глицерина постепенно увеличивайте примерно на 1 °С в минуту при постоянном перемешивании, чтобы она во всем объеме была одинаковой. За температуру начала открытия клапана принимайте ту, при которой ход основного клапана составит 0,1 мм.
* Термостат необходимо заменять, если температура начала открытия клапана отличается от 87±0,2 °С и ход клапана при повышении температуры до 102 оС составит менее 8 мм.
* Простейшая проверка работы термостата может быть осуществлена на ощупь непосредственно на автомобиле. После пуска холодного двигателя при исправном термостате отводящий патрубок радиатора должен нагреваться, когда температура охлаждающей жидкости достигнете?—92 °С.
Замена охлаждающей жидкости
* Снимите пробку расширительного бачка и откройте кран отопителя салона кузова. Открутите крепежные болты и снимите брызговик двигателя. Отверните две сливные пробки (в радиаторе и блоке цилиндров) и слейте жидкость из системы охлаждения. По окончании слива пробки заверните.
* Заполните систему чистой водой. Воду залейте в расширительный бачок, пока уровень не будет выше метки «MIN» на 25—30 мм, и заверните пробку расширительного бачка. Запустите двигатель, прогрейте на средней частоте вращения коленчатого вала до 90°С. При этой температуре циркуляция воды будет осуществляться по малому и большому кругам, будет промываться и радиатор. Остановите двигатель, слейте воду, заполните систему снова чистой водой и повторите промывку в том же порядке.
* Остановите двигатель, слейте воду и залейте в систему охлаждающую жидкость. Запустите двигатель, дайте поработать 1 —2 мин на холостом ходу для удаления воздушных пробок. После остывания двигателя проверьте уровень жидкости.
* В северных районах, где тосол продолжительное время находится в холодном состоянии, он стареет медленнее. Поэтому после окончания гарантийного срока службы тосол необходимо слить и проверить его качество.
* Если в жидкости нет грязи и масла и она сохранила голубой цвет, надо проверить ее плотность, при необходимости довести до нормы и использовать еще один год. После года эксплуатации проверку повторите.
Система смазки Масляный насос
* После разборки все детали промойте в керосине или бензине, продуйте сжатым воздухом и проверьте их состояние.
* Алюминиевая крышка в плоскости прилегания шестерен не должна иметь уступов. Поверхность должна быть плоской. При заметных износах зажмите крышку и отфрезеруйте поверхности до размера 13,5 мм. Максимальный съем металла не должен превышать 0,2 мм. Сальник коленчатого вала замените новым. При запрессовке сальника усилие прикладывайте как можно ближе к наружному диаметру сальника.
* Рабочие поверхности корпуса не должны иметь царапин. Предельный наружный диаметр под ведомую шестерню не должен превышать Ж 75,10 мм. Предельная минимальная ширина сегмента должна быть не менее 3,40 мм. При больших износах корпус насоса замените новым.
* Замерьте индикатором максимальные осевые зазоры, которые не должны превышать для ведущей шестерни 0,12 мм, для ведомой 0,15 мм.
* Если зазоры и размеры выходят за предельные значения, шестерни замените новыми.
* Проверьте также, не уменьшилась ли упругость пружины редукционного клапана, сравнивая полученные данные с требуемыми.
Промывка деталей вентиляции картера
* Снимите шланги вентиляции, открутите гайки крепления и снимите крышку головки блока цилиндров. Выверните два болта крепления корпуса маслоотделителя, снимите корпус и сетку. Промойте снятые детали бензином.
* У карбюратора очистите и промойте ацетоном или бензином штуцер шланга подвода картерных газов.
Замена масла
* Прогрейте двигатель, выверните сливную пробку и слейте масло в сосуд. Для полного слива масла выждите не менее 10 мин. Не снимая масляного фильтра, залейте промывочное масло до метки на указателе уровня масла. Запустите двигатель и дайте поработать ему 10 мин при минимальной частоте вращения коленчатого вала.
* Слейте полностью промывочное масло и снимите масляный фильтр. Поставьте новый фильтр и залейте 3,5 л моторного масла, соответствующего сезону эксплуатации.
* Если на распределительном валу не обнаружены смолистые отложения, то промывку системы можно не делать.
Система питания Терморегулятор
* Проверьте положение заслонки у снятого терморегулятора при температуре термосилового элемента +25 °С и +35 "С. В первом случае заслонка должна перекрывать патрубок подачи холодного воздуха, а во втором патрубок подачи подогретого воздуха. В противном случае правильность работы терморегулятора регулируйте вращением термосилового элемента и пломбируйте нанесением эмали на его шток.
Топливный бак
* Для очистки бака снимите датчик уровня топлива, промойте бак бензином. Тщательно осмотрите бак по линии стыка, чтобы убедиться в отсутствии течи.
* При обнаружении течи струей горячей воды промойте и пропарьте бак от остатков бензина, запаяйте бак мягким припоем. Паять можно только хорошо промытый и пропаренный бак, не содержащий паров бензина, чтобы исключить их воспламенение при пайке.
Топливный насос
* Проверьте подачу топлива насосом. Недостаточное наполнение карбюратора топливом может быть вызвано неисправностью топливного насоса, а также засорением или повреждением топливопроводов и топливного фильтра тонкой очистки.
* Для определения причины неисправности отсоедините шланг от нагнетательного патрубка 1 и с помощью рычага 8 ручной подкачки топлива проверьте, подается ли топливо (рис.3) Если топливо не подается, отсоедините шланг от впускного патрубка * и проверьте, создается ли разрежение на входе этого патрубка. Если разрежение есть, то повреждены или засорены топливопроводы или фильтр тонкой очистки. Если разрежения нет, неисправен топливный насос.
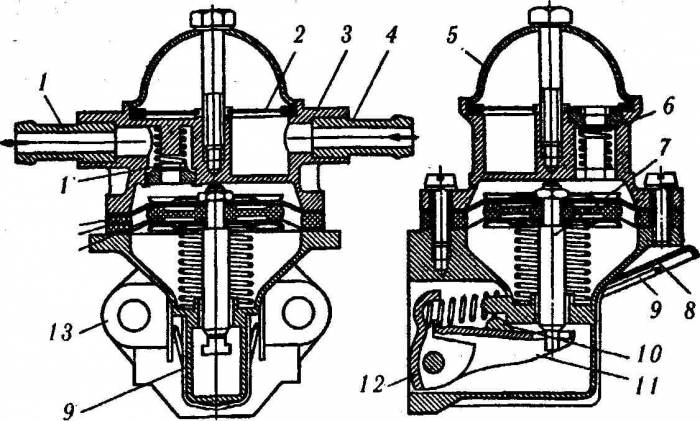
Рис.3. Топливный насос
* Топливный насос можно проверить на стенде. Вращая валик привода, имеющего эксцентриситет 1,25 мм, с частотой 2000 об/мин, проверьте производительность насоса, которая должна быть не менее 1 л/мин при 20 °С. Давление нагнетания при нулевой подаче топлива должно быть 0,21 —0,30 кгс/см2.
* При неисправности насос разберите и проверьте состояние деталей. Все детали должны быть промыты бензином и продуты сжатым воздухом. Трещины и обломы корпусных деталей недопустимы. Не допускается негерметичность впускного и нагнетательного клапанов. Впускной 4 и нагнетательный 1 патрубки (рис. 3) не должны проворачиваться в посадочных местах или иметь осевое смещение. Диафрагма не должна иметь прорывов, отслоений и затвердеваний. Фильтр должен быть чистым и без порывов. Уплотнительная кромка фильтра по периметру должна быть ровной. Клапаны насоса не должны заедать.
* После проверки все изношенные детали замените новыми. Поврежденные прокладки насоса всегда заменяйте новыми и при установке насоса смазывайте тонким слоем смазки.
Карбюратор
* Топливный фильтр промойте в бензине и продуйте сжатым воздухом. Проверьте состояние фильтра. Если фильтр или патрубок подвода топлива повреждены, замените их новыми.
* Промойте в бензине детали поплавкового механизма и проверьте их состояние. Поплавок не должен иметь повреждений. На уплотняющей поверхности игольчатого клапана и его седла не допускаются повреждения, нарушающие герметичность клапана. Клапан должен свободно перемещаться в своем гнезде, а шарик не должен зависать. Масса поплавка не должна быть более 6,23 г. Неисправные детали замените новыми.
* Очистите от масла и грязи крышку карбюратора и все отверстия и каналы. Промойте крышку в ацетоне или бензине и продуйте сжатым воздухом. Осмотрите уплотняющие поверхности крышки. Если имеются повреждения, замените крышку новой.
* Все детали пускового устройства очистите, промойте бензином и продуйте сжатым воздухом. Осмотрите детали, поврежденные замените новыми.
* Очистите от грязи и смолистых соединений жиклеры и эмульсионные трубки, промойте ацетоном или бен зином и продуйте сжатым воздухом. Нельзя очищать жиклеры металлическим инструментом или проволокой, а также протирать жиклеры и другие детали карбюратора ватой, тканью или ветошью, так как ворсинки могут засорить топливные и эмульсионные каналы. При сильном засорении можно очистить жиклеры иглой из мягкого дерева, смоченной ацетоном.
* Очистите корпус карбюратора от масла и грязи. Промойте его каналы ацетоном или бензином и продуйте сжатым воздухом. При необходимости каналы и эмульсионные трубки очистите специальными развертками. Осмотрите уплотняющие поверхности корпуса. При их повреждениях или деформациях замените корпус новым.
* Очистите детали ускорительного насоса, промойте бензином, продуйте сжатым воздухом. Проверьте легкость перемещения клапанов и движение подвижных элементов насоса (рычага, деталей диафрагмы). Заедания не допускаются. Диафрагма должна быть целой, без повреждений. Проверьте состояние уплотняющих поверхностей и прокладок. Поврежденные детали насоса замените новыми.
* Проверьте полную длину толкателя диафрагмы экономайзера мощностных режимов, включая головку толкателя. При длине менее 6 мм диафрагму в сборе с толкателем замените новыми.
* Проверьте работу механизма блокировки второй камеры, для чего рычаг управления воздушной заслонкой поворачивайте против часовой стрелки до полного закрытия заслонки. Затем поворачивайте рычаг управления дроссельными заслонками до полного открытия дроссельной заслонки первой камеры. При этом дроссельная заслонка второй камеры должна оставаться в закрытом положении. Затем поворачивайте рычаг управления воздушной заслонки до полного открытия заслонки, а рычаг управления дроссельными заслонками до полного открытия дроссельных заслонок. Если дроссельная заслонка второй камеры при этом не откроется, устраните неисправность. Причиной может быть заедание рычага блокировки второй камеры или отсоединение пружины рычага блокировки.
РЕГУЛИРОВКА ДВИГАТЕЛЯ Регулировка зазоров в механизме привода клапанов
* Зазор между кулачками распределительного вала и регулировочными шайбами на холодном двигателе должен быть 0,20 ±0,05 мм для впускных клапанов и 0,35 ± 0,05 мм для выпускных. Зазор на ВАЗ 2109 и некоторых иномарках регулируется подбором толщины регулировочных шайб. В запасные части поставляются регулировочные шайбы толщиной от 3 до 4,25 мм с интервалом через каждые 0,05 мм. Толщина шайбы маркируется на ее поверхности.
* Зазор регулируйте в следующем порядке. Снимите крышку головки цилиндров и переднюю защитную крышку зубчатого ремня. Выкрутите свечи зажигания и удалите масло из масляных ванн в головке цилиндров. Осмотрите поверхность кулачков распределительного вала: на них не должно быть задиров, раковин, износа и глубоких рисок. Установите на шпильки крепления крышки головки цилиндров приспособление для утапливания толкателей клапанов. Вместо приспособления можно пользоваться оправкой.
* Проверните коленчатый вал до совмещения установочных меток на шкиве и задней крышке зубчатого ремня, а затем доверните его еще на 40—50° (2,5— 3 зуба на шкиве распределительного вала). При этом, в 1 -м (от шкива) цилиндре будет фаза сгорания. Поворачивать коленчатый следует только по часовой стрелке, либо за болт крепления шкива привода генератора, либо приспособлением для проворачивания шкива распределительного вала за шкив распределительного вала. Не допускается проворачивание коленчатого вал за болт крепления шкива распределительного вала, так как можно повредить болт.
* Проверьте набором щупов зазоры у 1 -го и 3-го кулачков распределительного вала. Если зазор отличается от нормы, то приспособлением для утапливания толкателей клапанов или оправкой утапливайте толкатель клапана и фиксируйте его в нижнем положении, установив между краем толкателя и распределительным валом фиксатор.
* Приспособлением для замены регулировочной шайбы толкателей клапанов (стальная пластина с плоским магнитом) или щипцами с узкими губками удалите регулировочную шайбу и микрометром измерьте ее тол щину. Затем определите толщину новой шайбы по формуле Н=В+(А—С), где Н — толщина новой шайбы; А — замеренный зазор; В — толщина снятой шайбы; С — номинальный зазор.
* Установите в толкатель клапана новую регулировочную шайбу, уберите фиксатор для толкателей клапанов и еще раз проверьте зазор. Если он отрегулирован верно, то щуп толщиной 0,2 или 0,35 мм должен входить с легким защемлением. Последовательно проворачивая коленчатый вал на пол-оборота, что соответствует повороту метки на шкиве распределительного вала на 90°, регулируйте зазоры у остальных клапанов, соблюдая очередность работы цилиндров. После регулировки заливайте масло в масляные ванны головки цилиндров так, чтобы точки контакта кулачков с регулировочными шайбами оказались в масле. Установите крышку головки цилиндров и переднюю крышку зубчатого ремня.
Регулировка натяжения ремня привода распределительного вала
* Для натяжения ремня снимите переднюю защитную крышку зубчатого ремня и поверните коленчатый вал за болт крепления шкива привода генератора по часовой стрелке на два оборота. Проварачивать коленчатый вал следует только в сторону затягивания болта (по часовой стрелке). При натяжении ремня не допускается проворачивать коленчатый вал вращением за шкив распределительного вала или за болт его крепления.
* Проверьте натяжение ремня. Оно считается нормальным, если в средней части ветви между шкивами распределительного и коленчатого валов ремень закручивается вдоль на 90 ° усилием большого и указательного пальцев. Если усилие ниже нормы, ослабьте гайку крепления натяжного ролика, проверните его ось за шестигранную головку на 10— 15° против часовой стрелки и затяните гайку крепления оси.
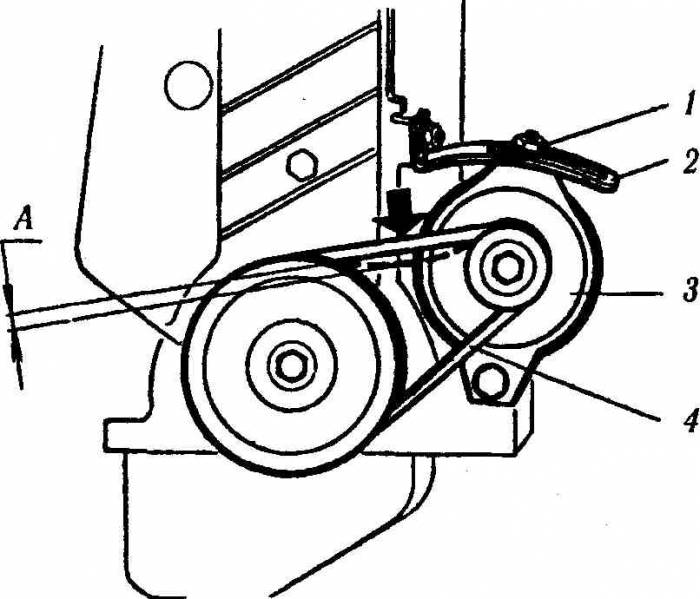
Рис. 4. Проверка натяжения ремня генератора
* Снова проверните коленчатый вал почасовой стрелке на два оборота и проверьте натяжение ремня. Если натяжение недостаточно, то повторите операцию. Если натяжение нормальное, то затяните гайку крепления оси натяжного ролика моментом 4 кгс • м и установите переднюю защитную крышку зубчатого ремня.
* При регулировке не следует допускать излишнего натяжения ремня, так как это значительно снижает срок его службы.
Регулировка натяжения ремня привода генератора
* Нормальный прогиб А ремня должен быть в пределах 8—10 мм при усилии 10 кгс (рис. 4). Для регулировки натяжения ремня 4 отпустите гайку крепления генератора к натяжной планке. Сместите генератор в сторону от двигателя (для увеличения натяжения) или к двигателю (для уменьшения натяжения) и затяните гайку. Проверните коленчатый вал на два оборота по часовой стрелке и проверьте натяжение ремня.
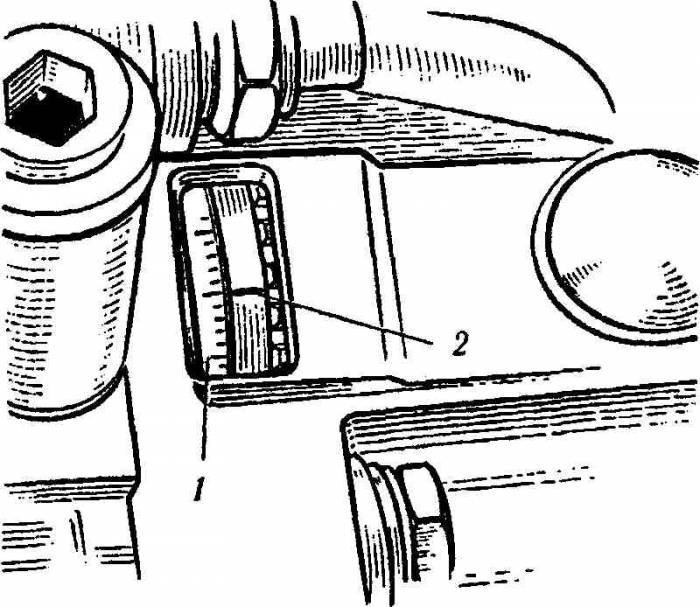
Рис.5. Метка на маховике и шкала на картере для установки момента зажигания
* Не следует допускать чрезмерного натяжения ремня, чтобы не вызвать повышения нагрузок на подшипники генератора.
Установка момента зажигания
* Угол опережения зажигания до верхней мертвой точки (в. м. т.) при частоте вращения коленчатого вала 750—800 об/мин должен быть (1 + 1)°.
* Для проверки на автомобиле момента зажигания имеется шкала 1 в люке картера сцепления и метка 2 на маховике (рис. 5). Одно деление шкалы соответствует Г поворота коленчатого вала. При совмещении метки на маховике со средним (длинным) делением шкалы поршни 1 -го и 4-го цилиндров находятся в в. м. т. При обкатке двигателя на стенде устанавливать момент зажигания можно с помощью меток на шкиве коленчатого вала и на передней крышке зубчатого ремня, показанных на рис.6. Метка 1 соответствует опережению зажигания на 5°, а метка 2 положению в. м. т. поршней 1 -го и 4-го цилиндров.
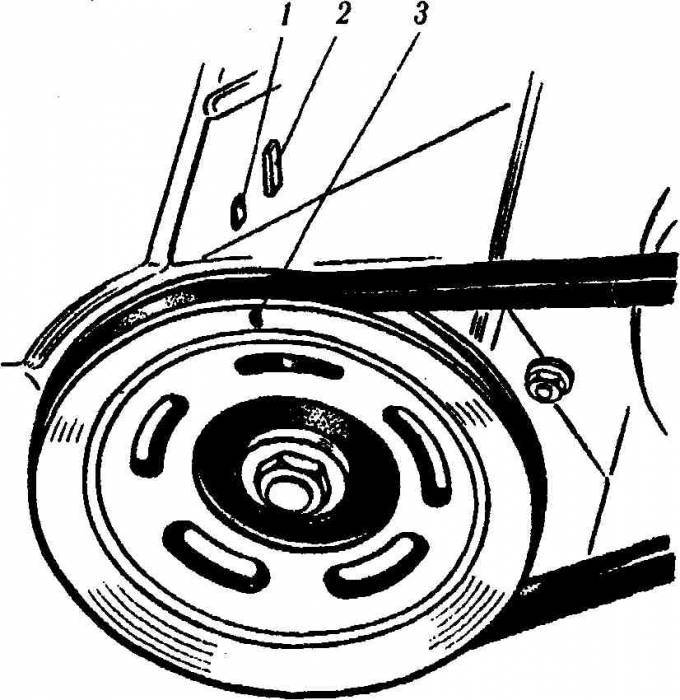
Рис.6. Метки для установки момента зажигания, расположенные на шкиве коленчатого вала и прередней крышке зубчатого ремня
* Проверьте и установите момент зажигания с помощью стробоскопа, действуя в следующем порядке. Соедините зажим «плюс» стробоскопа с клеммой «плюс», зажим массы с клеммой «минус» аккумуляторной батареи, а зажим датчика стробоскопа присоедините к проводу высокого напряжения 1 -го цилиндра. Отключите вакуумное опережение зажигания. Запустите двигатель и направьте мигающий поток света стробоскопа в люк картера сцепления. Если момент зажигания установлен правильно, то на холостом ходу двигателя метка на маховике должна на одно деление не доходить до среднего деления шкалы 1 (см. рис.).
* Для регулировки момента зажигания остановите двигатель, ослабьте гайки крепления датчика-распределителя зажигания и поверните его на необходимый угол. Для увеличения угла опережения зажигания корпус датчика-распределителя следует повернуть по часовой стрелке, а для уменьшения—против (если смотреть со стороны крышки датчика-распределителя зажигания). Затяните гайки крепления и снова проверьте установку момента зажигания.
* Для удобства регулировки момента зажигания на фланце датчика-распределителя имеются деления и знаки « + » и « —», а на корпусе вспомогательных агрегатов — установочный выступ. Одно деление на фланце соответствует примерно пяти градусам поворота коленчатого вала.
Регулировки карбюратора Установка уровня топлива в поплавковой камере
* Необходимый для нормальной работы карбюратора уровень топлива обеспечивается правильной установкой исправных элементов запорного устройства.
* Правильность установки поплавка проверяется калибром. Размеры калибра приведены на рис. 7. Калибр установите перпендикулярно крышке с прокладкой (рис. 7.) Крышку необходимо держать горизонтально поплавками 1 вверх. Между калибром 4 по контуру и поплавками должен быть зазор не более 1 мм. При необходимости его регулируют подгибанием язычка и рычагов поплавка 5. Опорная поверхность язычка должна быть перпендикулярна оси игольчатого клапана и не должна иметь вмятин и забоин.
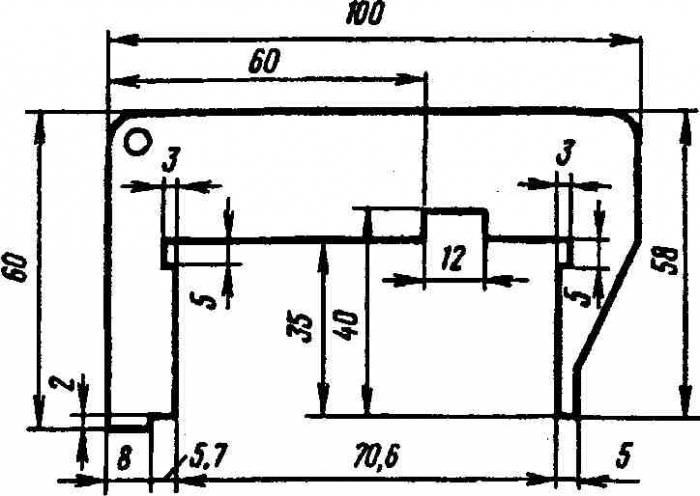
Рис. 7. Установка уровня топлива в поплавковой камере карбюратора 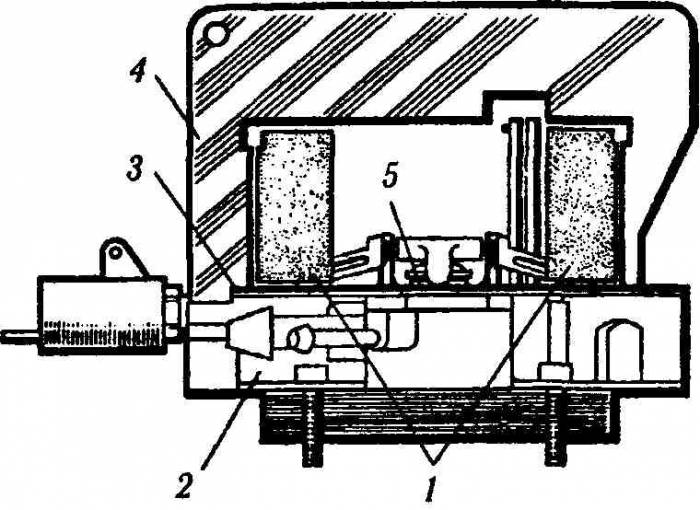
Рис.8. Схема пускового устройства карбюратора
Регулировка пускового устройства
Схема пускового устройства приведена на рис. 8.
* При повороте рычага 4 (см. схему пускового устройства карбюратора) управления воздушной заслонкой 5 до отказа против часовой стрелки воздушная заслонка должна быть полностью закрыта под действием пружины 7. Если заслонка не закрыта, устраните причину заедания.
* При полностью закрытой воздушной заслонке нажмите вручную на шток 3 пускового устройства до упора. При этом воздушная заслонка должна открываться на 3+0,2 мм (пусковой зазор В). При необходимости регулируйте зазор винтом 2.
* Дроссельная заслонка 10 первой камеры при полностью закрытой воздушной заслонке должна быть приоткрыта на 0,88 мм (пусковой зазор Д). Регулируйте этот зазор винтом 9.
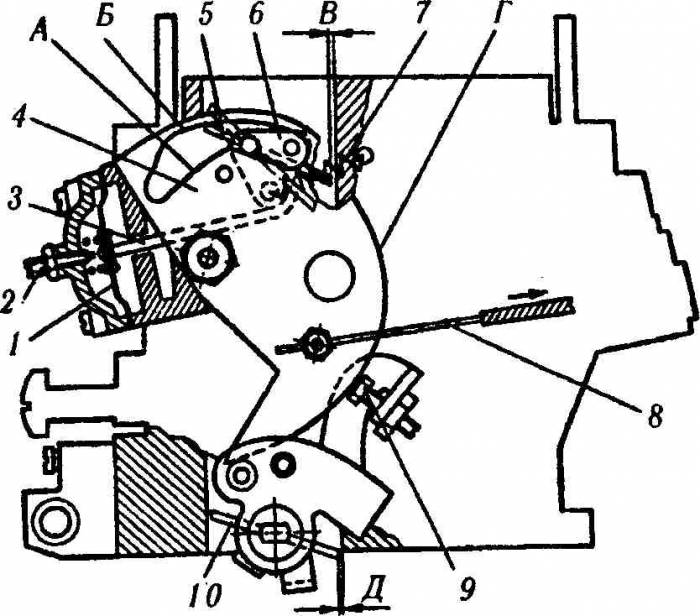
Рис. 9. Привод управления карбюратора
1 —педаль управления дроссельными заслонками (акселератор); 2 — возвратная пружина; 3 — прокладка упора педали; 4 — кронштейн; 5 — втулка; б — стопорная стопа; 7 — наконечник троса; 8 — рукоятка управления воздушной заслонкой; 9 — стопорная пружина; 10 — оболочка тяги; 11 — оболочка троса; 12 — кронштейн регулирующего наконечника; 13 — регулировочные гайки; 14 — тяга привода воздушной заслонки; 15 — сектор упраления дроссельными заслонками; 16 — рычаг управления воздушной заслонки.
Регулировка привода карбюратора
* При полностью нажатой педали 1 (см. рис.9) управления дроссельными заслонками, дроссельная заслонка первой камеры должна быть полностью открыта и сектор 15 не должен иметь дополнительного хода. При отпущенной педали дроссельная заслонка должна быть полностью закрыта. Если этого нет, регулируйте положение педали и дроссельной заслонки регулировочными гайками 13 на переднем наконечнике троса привода.
* В приводе воздушной заслонки (рис.9) оболочку 10 тяги 14 закрепите так, чтобы она выступала на 40 мм. Тягу 14 крепите на рычаге 16 управления воздушной заслонкой, чтобы при вытянутой рукоятке 8 воздушная заслонка была полностью закрыта, а при утопленной рукоятке — полностью открыта.
Регулировка холостого хода двигателя
* Элементы регулировки холостого хода включают регулировочный винт качества (состава) смеси и регулировочный винт количества смеси. Регулировочный винт качества с уплотнительным кольцом закрыт заглушкой. Для доступа к винту необходимо сломать заглушку. В некоторых иномарках рекомендуют ввинтить в заглушку шуруп и за этот шуруп клещами вытащить заглушку.
* Регулировку холостого хода необходимо выполнять на прогретом двигателе (температура охлаждающей жидкости должна быть 90—95°С) с отрегулированными зазорами в газораспределительном механизме, с правильно установленным углом опережения зажигания и при полностью открытой воздушной заслонке. Регулировочным винтом количества установите по тахометру стенда частоту вращения коленчатого вала двигателя в пределах 750—800 об/мин. Затем регулировочным винтом качества (состава) смеси добейтесь концентрации окиси углерода (СО)+ в отработавших газах в пределах 0,5— 1,2% при данном положении винта количества (концентрация СО приводится к 20 °С и 760 мм рт. ст.). Винтом количества установите частоту вращения коленчатого вала до 750—800 об/мин, при необходимости регулировочным винтом качества опять подрегулируйте концентрацию СО до 0,5—1,2%.
* По окончании регулировки резко нажмите на акселератор и отпустите его; двигатель при этом должен без перебоев увеличить частоту вращения коленчатого вала, а приуменьшении ее — не заглохнуть. В случае остановки двигателя винтом количества увеличивайте частоту вращения коленчатого вала в пределах 750—800 об/мин.
* После регулировки установите в отверстие для регулировочного винта новую пластмассовую заглушку.
ОБРАБОТКА ДВИГАТЕЛЯ ПОСЛЕ РЕМОНТА
* Отремонтированный двигатель подвергается стендовым испытаниям (обкатке) без нагрузки по следующему циклу: на частоте вращения 750—800 об/мин— 2 мин; 1000 — 3; 1500 — 4; 2000 об/мин—5 мин.
* Установив на стенде и запустив двигатель, проверьте: нет ли течи охлаждающей жидкости или топлива между сопрягаемыми деталями, из соединений трубопроводов и через прокладки; нет ли подтекания масла из-под уплотнительного кольца масляного фильтра и через прокладки; давление масла; установку момента зажигания; частоту вращения коленвала на холостом ходу; герметичность соединения карбюратора с впускным трубопроводом; нет ли посторонних стуков.
* Если обнаружатся посторонние стуки или неисправности, остановите двигатель, устраните их, а затем продолжайте испытания.
* При подтекании масла через прокладку между масляным картером двигателя и блоком цилиндров подтяните болты с рекомендуемым моментом. Если течь масла не прекращается, проверьте качество прокладок и при необходимости замените их.
* При подтекании масла через прокладку между крышкой и головкой блока цилиндров проверьте прокладку и резиновые втулки на шпильках крепления крышки головки цилиндров. При необходимости замените прокладку и втулки.
* Так как после ремонта двигателя его детали еще не приработались и трение рабочих поверхностей новых деталей оказывает значительное сопротивление вращению, необходим определенный период приработки. Указанное, в особенности, относится к тем двигателям, на которых были заменены поршни, вкладыши шатунных и коренных подшипников, перешлифованы шейки коленчатого вала, а также отхонингованы цилиндры.
* Поэтому во время обкатки отремонтированного двигателя не следует доводить его до максимальных нагрузок. Обкатка двигателя на автомобиле должна продолжаться с соблюдением тех скоростей движения, которые рекомендуются для нового автомобиля.
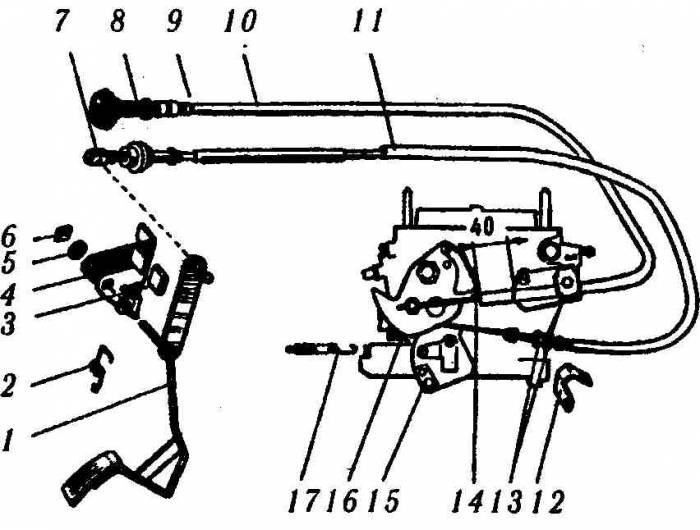
|